Moisture facts: Humidity and installing hardwood flooring
Thursday, July 7, 2022 10:02 AM
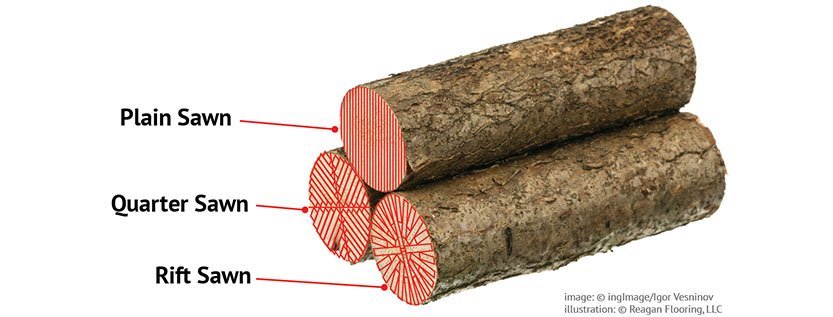
As we all know, wood is a hygroscopic material, meaning it shrinks or swells depending on moisture levels. You can see the directions of expansion and contraction in the different cuts of hardwood as they gain or lose moisture. Because of the direction of the growth rings, plainsawn boards change in dimension across the width of the board, and the wider the board, the more the potential for dimensional change.
Quartersawn and riftsawn boards, change size in the thickness.
Wood veneers are either plain sawn or rotary cut. The expansion or shrinkage of the wood varies:
High water/cement, admixtures ratio will take much longer to emit the excess moisture content.
Ambient site conditions are poor and do not allow for adequate air movement. Low temperatures or high relative humidity levels in the air. These conditions limit the ability of the concrete slab to get rid of (evaporate) the excess moisture.
If an adequate moisture barrier has not been installed under the slab, moisture may be accessing the slab from various sources, including groundwater, defective plumbing or improper drainage around the slab
The concrete slab surface has been aggressively hard troweled, sealing the concrete surface and the pathways that allow moisture to move to the surface and evaporate.
Surface treatment is probably the biggest culprit. This includes hard troweling, curing compounds and sealers, poor site conditions when moisture testing.
Calcium Chloride Tests only test the surface of the concrete. Relative Humidity Testing is reading the amount of moisture internally through the concrete.
Moisture related problems in flooring are more prevalent today than they used to be. Several factors are responsible for that and perhaps the most prevalent are:
A misunderstanding is that moisture problems will not occur if there is a “vapor barrier” in place be-neath the slab. Most slabs today that have problems also have a “vapor barrier” that was installed at the time of construction.
Due to field conditions, conventional “vapor barriers” essentially become ineffective as true barriers the day they are installed. In almost every slab, holes for column footers as well as electrical, plumbing and other penetrations through the underside of the slab. Unless all seams are overlapped and sealed, the seams themselves represent another potential for moisture intrusion. Ultimately, puncture damage do to normal abuse and wear at the time the concrete is placed may be the largest single factor leading to ineffective vapor barriers.
A 4″ slab poured at .50 Water/Cement ratio evaporates more than a ½ gallon of moisture per square foot.Concrete slabs, properly prepared and poured under functional HVAC control typically take one inch per month to reach moisture levels suitable for “normal” floor covering installation. Rewetting the slab resets the drying time clock by several weeks.”
Quartersawn and riftsawn boards, change size in the thickness.
Wood veneers are either plain sawn or rotary cut. The expansion or shrinkage of the wood varies:
- According to the species.
- Where the cut comes from in the log. The heart wood is harder than the outer part where the sap wood is found.
- According to the cutting season. Winter wood is generally harder than spring/summer wood.
- According to the cut (see illustration above).
- Plain Sawn: The log is sliced from top to bottom or left to right. This generally used method is more economical and provides the best yield, but since the cut is across the rings, these veneers will expand easily.
- Quarter Sawn: The log is divided in quarter and the cut is made across the grain. The waste factor is higher with this cutting method but the stability of the wood is better than with the plain sawn cut.
- Rotary Cut: The log is soaked in water then peeled like unrolling a roll of paper towels.
How can a concrete slab still have excessively high relative humidity reading six months after it was poured?
High water/cement, admixtures ratio will take much longer to emit the excess moisture content.
Ambient site conditions are poor and do not allow for adequate air movement. Low temperatures or high relative humidity levels in the air. These conditions limit the ability of the concrete slab to get rid of (evaporate) the excess moisture.
If an adequate moisture barrier has not been installed under the slab, moisture may be accessing the slab from various sources, including groundwater, defective plumbing or improper drainage around the slab
The concrete slab surface has been aggressively hard troweled, sealing the concrete surface and the pathways that allow moisture to move to the surface and evaporate.
How can a calcium chloride reading be low and the relative humidity reading be so high?
Surface treatment is probably the biggest culprit. This includes hard troweling, curing compounds and sealers, poor site conditions when moisture testing.
Calcium Chloride Tests only test the surface of the concrete. Relative Humidity Testing is reading the amount of moisture internally through the concrete.
Moisture related problems in flooring are more prevalent today than they used to be. Several factors are responsible for that and perhaps the most prevalent are:
- Fast track construction resulting in reduced slab drying time prior to flooring installation
- Construction specifications for on grade slabs (use of curing and sealing compounds)
- Increased use of light weight concrete on above grade slabs
- The use of non-vented pans in concrete construction (dries from 1 side only)
A misunderstanding is that moisture problems will not occur if there is a “vapor barrier” in place be-neath the slab. Most slabs today that have problems also have a “vapor barrier” that was installed at the time of construction.
Due to field conditions, conventional “vapor barriers” essentially become ineffective as true barriers the day they are installed. In almost every slab, holes for column footers as well as electrical, plumbing and other penetrations through the underside of the slab. Unless all seams are overlapped and sealed, the seams themselves represent another potential for moisture intrusion. Ultimately, puncture damage do to normal abuse and wear at the time the concrete is placed may be the largest single factor leading to ineffective vapor barriers.
A 4″ slab poured at .50 Water/Cement ratio evaporates more than a ½ gallon of moisture per square foot.Concrete slabs, properly prepared and poured under functional HVAC control typically take one inch per month to reach moisture levels suitable for “normal” floor covering installation. Rewetting the slab resets the drying time clock by several weeks.”